The FrankenBrick Smart BMW build
Moderators: Dan J, Diesel Dave, Crazymanneil, Stuart
- Crazymanneil
- Site Admin
- Posts: 566
- Joined: Sat Dec 02, 2006 10:10 pm
- Location: Bangor, Northern Ireland
- Contact:
Re: The FrankenBrick Smart BMW build
Hey just saw this on Facebook. Looks like you are making some great progress and plenty of build info. I am sure you will get on well with this project.
The ECU I used (and others like the marine guys) is no longer available unfortunately. It was nice and small but also quite restrictive in what you can do with it. Your ECU should be pretty flexible as I understand it. Megasquirt etc are unsuitable as you have found. SC really is the only choice though I have no experience of them. There might be quite a bit of software tweaking to do after you get it running but its nice to have the flexibility. There is one other company that makes a standalone common-rail ecu but it is like 6000 euro.
Don't forget a fuel filter. These engines have very small injector orifices and don't like any dirt.
Neil
The ECU I used (and others like the marine guys) is no longer available unfortunately. It was nice and small but also quite restrictive in what you can do with it. Your ECU should be pretty flexible as I understand it. Megasquirt etc are unsuitable as you have found. SC really is the only choice though I have no experience of them. There might be quite a bit of software tweaking to do after you get it running but its nice to have the flexibility. There is one other company that makes a standalone common-rail ecu but it is like 6000 euro.
Don't forget a fuel filter. These engines have very small injector orifices and don't like any dirt.
Neil
Smart engined 800cc turbo diesel triumph tiger. 100mpg (imp)
Belfast to Kathmandu overland, 2010/2011 - http://www.suckindiesel.com
Bangkok to Sydney ???
Belfast to Kathmandu overland, 2010/2011 - http://www.suckindiesel.com
Bangkok to Sydney ???
-
- I luv the smell of Diesel...
- Posts: 224
- Joined: Sat Oct 24, 2015 2:20 pm
- Location: North Wales, UK
Re: The FrankenBrick Smart BMW build
Thanks Neil.
I am going to use the original K 100 in tank pump and canister filter because obviously, in the original petrol driven bike those injectors didn’t like dirt either. The fuel pump runs at about 3-4 bar which I am told is fine to feed the injector pump.
It’s a shame the other ECU is “out of print”. I believe that the SC is extremely flexible although with the Injector Driver Module it’s not small. Simon (who has been very helpful answering my stupid questions) says that there is already a map in there which may only want tweaking. I will cross that bridge when I come to it.
If it had been €6000 I would never have started and I would have ended up waiting for a Daihatsu Charade motor.
I am just waiting for the plasma cut parts to arrive to brace the front of the frame and to make the front engine mountings. I should have those tacked together by weekend. My welder is not fantastic so I’m going to just do the tacking and use a friend of mine’s commercial machine to do the bulk of the welding.
I have now finished my latest incarnation of the exhaust manifold adapter (turning it upside down) and I am really really pleased with the fit. I’m going to do a little bit of milling around the edges to tidy it up this evening and hope to have it fitted later. Photos to follow along with other bits.
Here below is my update which actually predates this post of yours in time but obviously not in posting. There are photos to be added but I haven’t got time at the at the moment so will edit later.
-------------------------------------------------------------------------------------------------------------------------------------------------------------------------------------------------------------------------------------------------
I have got a little bit of work to do on the frame yet but took some time out to play around with the exhaust.
I screwed up making the original exhaust manifold adapter plate (if you have been paying attention, you will remember that the exhaust manifold needs to be turned upside down)
Here it is in the original position.
43
However, by measuring a couple of the holes in the wrong place and assuming all the holes were equi distant (which they are not). However, notwithstanding that, it wasn’t really thick enough because I need to replace the whole exhaust out from a plastic water coolant pipe. I also want to put a heat shield between the manifold and the pipe in with my original plate which 10 mm thick, (beautiful stainless steel) it just didn’t cut the mustard. So I went completely the other way and have gone for 25 mm thick aluminium which I got from eBay for 15 quid (£15 GBP). It was just the right size blank although I’m going to trim the edges to make it look a bit more “thought about”.
I then had an inspiration about marking it out. I have the drawings produced in CAD for laser cutting of the original bits and it occurred to me that I could use the same process for the holes. So, I got the guy that did the CAD drawings to produce one, not just for the blank, but also with the holes. Now it seems that when these guys do CAD drawings they like to produce them full-size. I also wanted PDFs so that I can see what it looks like because I can’t read the CAD files. Lo and behold, the PDFs are full-size. A quick tape measure confirm that. The beauty of CAD is that it is completely accurate and therefore I printed the PDF out full-size, sprayed a little glue on and stuck it onto the aluminium blank. Centre pop through the holes and got working with the drill.
This is the impressive bit.
The manifold goes on to 8 mm studs (actually, it will eventually be held on with counter bored Allen screws but more of that later) so I drill the holes out 8.5 mm. Remember, all I have done this stage is stuck the paper CAD drawing onto the aluminium blank. With all the holes drilled, it was a perfect fit over the 8 mm studs and so accurate was it that even though the holes are only 0.5 mm larger, than the studs over which they are going, there was still a little bit of play. A fantastic result.
Here are a couple of pics of the rather battered -looking drawings still in place after the holes had been drilled and the ones that needed tapping M8 to take the studs, tapped.
DSC04365
DSC04374
Just in case you’ve forgotten, plate is held on to the cylinder head M8 Allen screws in a counter bore. That produces a flat surface which the manifold can be attached to. The manifold, turned upside down is then fastened on to the plate.
The position of the upsidedown manifold is located with M8 tapped holes which used to go into the cylinder head now, in reverse position, (upsidedown) go into the plate. Simples.
Here it is, trial fitted and fettled.I cut the plate by “hand” using a 1 mm aluminium cutting disc in an angle grinder or rather I used 1 ½ discs. They really do last a long time provided you have the aluminium material discs. If you have the steel material cutting discs, and use them on aluminium, they last no time at all. I then finished it with a flap wheel and then, just to make it look a bit prettier, I squared the edges up on the milling machine. It wasn’t really needed but did just square the edges off. I then polished the edges and rounded the top corners on a polishing wheel. I got very black, very dirty, and there was lots of grit and dust everywhere. But, I did it myself!The black plastic thing held in with two screws and two pipes going downwards is a water feed from the block to the oil cooler which is one of those where the oil is cooled by the water. When the manifold is turned upside down, I think it comes a little close to these pipes which, although there filled with water, are nonetheless plastic and because they are close to the turbo, I wasn't very happy about it which is why I put the heat shield in which you will read about later
DSC04381
DSC04380
When the exhaust manifold turned upside down, the turbo is also turned upside down oil feed and drainer in the wrong place.Ignore the blue circle on the right. They are holes which do something on the car which I have now tapped M8 for top front engine mountings.
The red circle is the turbo oil drain and the thin pipe just to the left is the turbo oil feed.Ignore the blue circle on the right. That's just indicating some holes which are drilled in the engine which I later tapped M8 to take the engine mounting on the right-hand side. Nice and convenient!
The oil feed comes from a gallery in the engine block into the top of the turbo housing.
The oil drain comes from the bottom of the turbo housing through the large pipe into an adapter plate on the engine block which is just out of view. It's not possible to use that when the manifold has been turned upside down so in my case,So the adapter plate on the engine block is just going to become a crankcase breather.
As you appreciate, when the manifold is turned upside down turbo is also upside down and the reason that the turbo needs rotating through 180° is that the oil feed has moved to the bottom and the drain to the top which is totally unsatisfactory. Rotating the turbo changes that put all the pipework needs changing as well.
The thinner oil pipe (vertical in the photograph) needs a lot of bending to get it eventually back into the right place.
43
I turned the turbo exhaust body housing through 180° to bring the oil feed and oil drain into the correct position. Here is the refettled oil drain pipe which will drain into the dipstick tube. I found 12mm plumbing fittings on ebay which make modifying the dipsick tube easy. Pic to follow when all in place
DSC04384
However turning the turbo through almost 180 deg means that the turbo outlet is pointing in completely the wrong direction, towards the floor whereas it needs to point upwards to go over the top of the engine to be linked to the inlet manifold. There is no intercooler remember. So, just the turbo turbine aluminium housing needs turning back through hundred and 80° so the turbine outlet however this means the wastegate actuator is in the wrong place to operate the wastegate and therefore there needs to be another adapter plate the wastegate into the correct place. I did a little bit of playing around with this and although the plate isn’t the ideal shape (a second one would be) it’s not worth changing just to make it look prettier.
Turning the turbo three 180° on the exhaust manifold was actually quite easy although as the three mounting holes are not Equi-distant around the outside, when the turbo has been turned, only 2 of them line up. I got around the third one by making up a small bracket from a piece of angle iron which I think neatly did the job rather well. I think that other builders and indeed Eva Track just use the 2 holes but I wasn’t comfortable with it.
47
46
Of course, it also meant changing the oil feed pipe which fortunately is really thick wall and (although I was still very careful with it), I managed to bend it without kinking it and got it to fit in good order (I think!).
Here it is in approximately the position that it will end up.
DSC04387
I am going to use the original K 100 in tank pump and canister filter because obviously, in the original petrol driven bike those injectors didn’t like dirt either. The fuel pump runs at about 3-4 bar which I am told is fine to feed the injector pump.
It’s a shame the other ECU is “out of print”. I believe that the SC is extremely flexible although with the Injector Driver Module it’s not small. Simon (who has been very helpful answering my stupid questions) says that there is already a map in there which may only want tweaking. I will cross that bridge when I come to it.
If it had been €6000 I would never have started and I would have ended up waiting for a Daihatsu Charade motor.
I am just waiting for the plasma cut parts to arrive to brace the front of the frame and to make the front engine mountings. I should have those tacked together by weekend. My welder is not fantastic so I’m going to just do the tacking and use a friend of mine’s commercial machine to do the bulk of the welding.
I have now finished my latest incarnation of the exhaust manifold adapter (turning it upside down) and I am really really pleased with the fit. I’m going to do a little bit of milling around the edges to tidy it up this evening and hope to have it fitted later. Photos to follow along with other bits.
Here below is my update which actually predates this post of yours in time but obviously not in posting. There are photos to be added but I haven’t got time at the at the moment so will edit later.
-------------------------------------------------------------------------------------------------------------------------------------------------------------------------------------------------------------------------------------------------
I have got a little bit of work to do on the frame yet but took some time out to play around with the exhaust.
I screwed up making the original exhaust manifold adapter plate (if you have been paying attention, you will remember that the exhaust manifold needs to be turned upside down)
Here it is in the original position.

However, by measuring a couple of the holes in the wrong place and assuming all the holes were equi distant (which they are not). However, notwithstanding that, it wasn’t really thick enough because I need to replace the whole exhaust out from a plastic water coolant pipe. I also want to put a heat shield between the manifold and the pipe in with my original plate which 10 mm thick, (beautiful stainless steel) it just didn’t cut the mustard. So I went completely the other way and have gone for 25 mm thick aluminium which I got from eBay for 15 quid (£15 GBP). It was just the right size blank although I’m going to trim the edges to make it look a bit more “thought about”.
I then had an inspiration about marking it out. I have the drawings produced in CAD for laser cutting of the original bits and it occurred to me that I could use the same process for the holes. So, I got the guy that did the CAD drawings to produce one, not just for the blank, but also with the holes. Now it seems that when these guys do CAD drawings they like to produce them full-size. I also wanted PDFs so that I can see what it looks like because I can’t read the CAD files. Lo and behold, the PDFs are full-size. A quick tape measure confirm that. The beauty of CAD is that it is completely accurate and therefore I printed the PDF out full-size, sprayed a little glue on and stuck it onto the aluminium blank. Centre pop through the holes and got working with the drill.
This is the impressive bit.
The manifold goes on to 8 mm studs (actually, it will eventually be held on with counter bored Allen screws but more of that later) so I drill the holes out 8.5 mm. Remember, all I have done this stage is stuck the paper CAD drawing onto the aluminium blank. With all the holes drilled, it was a perfect fit over the 8 mm studs and so accurate was it that even though the holes are only 0.5 mm larger, than the studs over which they are going, there was still a little bit of play. A fantastic result.
Here are a couple of pics of the rather battered -looking drawings still in place after the holes had been drilled and the ones that needed tapping M8 to take the studs, tapped.


Just in case you’ve forgotten, plate is held on to the cylinder head M8 Allen screws in a counter bore. That produces a flat surface which the manifold can be attached to. The manifold, turned upside down is then fastened on to the plate.
The position of the upsidedown manifold is located with M8 tapped holes which used to go into the cylinder head now, in reverse position, (upsidedown) go into the plate. Simples.
Here it is, trial fitted and fettled.I cut the plate by “hand” using a 1 mm aluminium cutting disc in an angle grinder or rather I used 1 ½ discs. They really do last a long time provided you have the aluminium material discs. If you have the steel material cutting discs, and use them on aluminium, they last no time at all. I then finished it with a flap wheel and then, just to make it look a bit prettier, I squared the edges up on the milling machine. It wasn’t really needed but did just square the edges off. I then polished the edges and rounded the top corners on a polishing wheel. I got very black, very dirty, and there was lots of grit and dust everywhere. But, I did it myself!The black plastic thing held in with two screws and two pipes going downwards is a water feed from the block to the oil cooler which is one of those where the oil is cooled by the water. When the manifold is turned upside down, I think it comes a little close to these pipes which, although there filled with water, are nonetheless plastic and because they are close to the turbo, I wasn't very happy about it which is why I put the heat shield in which you will read about later


When the exhaust manifold turned upside down, the turbo is also turned upside down oil feed and drainer in the wrong place.Ignore the blue circle on the right. They are holes which do something on the car which I have now tapped M8 for top front engine mountings.
The red circle is the turbo oil drain and the thin pipe just to the left is the turbo oil feed.Ignore the blue circle on the right. That's just indicating some holes which are drilled in the engine which I later tapped M8 to take the engine mounting on the right-hand side. Nice and convenient!
The oil feed comes from a gallery in the engine block into the top of the turbo housing.
The oil drain comes from the bottom of the turbo housing through the large pipe into an adapter plate on the engine block which is just out of view. It's not possible to use that when the manifold has been turned upside down so in my case,So the adapter plate on the engine block is just going to become a crankcase breather.
As you appreciate, when the manifold is turned upside down turbo is also upside down and the reason that the turbo needs rotating through 180° is that the oil feed has moved to the bottom and the drain to the top which is totally unsatisfactory. Rotating the turbo changes that put all the pipework needs changing as well.
The thinner oil pipe (vertical in the photograph) needs a lot of bending to get it eventually back into the right place.

I turned the turbo exhaust body housing through 180° to bring the oil feed and oil drain into the correct position. Here is the refettled oil drain pipe which will drain into the dipstick tube. I found 12mm plumbing fittings on ebay which make modifying the dipsick tube easy. Pic to follow when all in place

However turning the turbo through almost 180 deg means that the turbo outlet is pointing in completely the wrong direction, towards the floor whereas it needs to point upwards to go over the top of the engine to be linked to the inlet manifold. There is no intercooler remember. So, just the turbo turbine aluminium housing needs turning back through hundred and 80° so the turbine outlet however this means the wastegate actuator is in the wrong place to operate the wastegate and therefore there needs to be another adapter plate the wastegate into the correct place. I did a little bit of playing around with this and although the plate isn’t the ideal shape (a second one would be) it’s not worth changing just to make it look prettier.
Turning the turbo three 180° on the exhaust manifold was actually quite easy although as the three mounting holes are not Equi-distant around the outside, when the turbo has been turned, only 2 of them line up. I got around the third one by making up a small bracket from a piece of angle iron which I think neatly did the job rather well. I think that other builders and indeed Eva Track just use the 2 holes but I wasn’t comfortable with it.


Of course, it also meant changing the oil feed pipe which fortunately is really thick wall and (although I was still very careful with it), I managed to bend it without kinking it and got it to fit in good order (I think!).
Here it is in approximately the position that it will end up.

Last edited by touchwoodsden on Sun Feb 21, 2016 10:52 pm, edited 3 times in total.
Merc Estate
BRA CX 3
2 CV Dolly
2 x 250 MZs
1 x 125 4 stroke MZ
2 x 301 MZ
1 x Enfield Himalayan
1x Monkey bike
1 x Honda CT125
1 x Campervan Vivaro
1 x MZ Es250/1 and sidecar
1 x Cat
2 x Parrots
BRA CX 3
2 CV Dolly
2 x 250 MZs
1 x 125 4 stroke MZ
2 x 301 MZ
1 x Enfield Himalayan
1x Monkey bike
1 x Honda CT125
1 x Campervan Vivaro
1 x MZ Es250/1 and sidecar
1 x Cat
2 x Parrots
-
- I luv the smell of Diesel...
- Posts: 224
- Joined: Sat Oct 24, 2015 2:20 pm
- Location: North Wales, UK
Re: The FrankenBrick Smart BMW build
Latest update, all done on the evening of 19 February 2016.
I had the engine mounting plate plasma cut. I wanted to compare with laser cutting. Yes, I could have cut them out myself quite quickly using a 1 mm stainless steel type material cutting disc in an angle grinder and it would have been quicker than making them but firstly, I needed the sheet steel (which I didn’t have) and secondly, I didn’t want the grit and dust everywhere. I have had enough of that.
I did have the pattern for them drawn in CAD and as I did with the exhaust manifold adapter, I stuck the full-size PDF of the CAD drawing onto the plate, marked through the holes and drilled. You can see the remnants of the paper drawing in this photograph of the left-hand engine mount.
The round steel through the frame lug is simply a piece of bar for lining up purposes. There is yet to be a boss welded onto the triangular plate and the engine mountings in the lugs which are metalastic type, I’m going to buy new ones. The old ones were 30 years old and in any event, they had got a little “warm” (to say the least (!) when I heated the tubes up for bending.
Here is the left-hand one
DSC04390
DSC04394
still the Left-hand one. The thick plate/casting you can see under the mounting is part of the original Smart. There was an additional lug on the front which I cut off which is why the front is now a flat face. The alternative was to mount the 8 mm plate straight onto the engine block but that would have meant a long boss on the steel plate which would then have need a triangulation. I think the original Smart lump, although heavy, does a good job.
DSC04403
the right-hand one
DSC04398
DSC04399
DSC04404
I had removed the triangular braces which go in here to facilitate bending the front frame down tube. Here are my new and somewhat larger ones. The hole in the centre is just for lightening and aesthetic purposes. The plates are 3 mm which in hindsight is probably a little heavy. Still, I’m not going to get them remade in 2 mm.
DSC04395
I have mentioned many times that the exhaust manifold needed turning upside down. This is probably involved as much work and fannying around as any other single job.
When the turbo is turned upside down, the oil feed pipe that you see here had to moved to the top and the drain to the bottom. This photograph is in the relocated position.
DSC04400
Therefore, you have to remove the turbine housing (the alloy part) turn the turbo through 180° ° approximately. This then means that the wastegate actuator is in the wrong place and it won’t fit on the original lugs. I therefore had the circular plate laser cut from 4 mm stainless steel to remount the actuator. The reason for the rather odd bump on the outside is that I wasn’t quite sure where the actuator would fit so I left a chunk of extra metal so that I could play around with where the holes went. In the end, my design was way out. I also had to fit it twice in 2 different positions which accounts for the extra set of M 6 holes.
DSC04405
When it was first fitted the whole mechanism was quite stiff and it transpires that the actuator (for some bizarre reason) is on a slight angle. You can’t see very well in this photograph but there is a slight angle at the bottom of the circular plate. Vice + hammer + stainless steel part = bend.
DSC04406
You can’t see the oil feed pipe very well here but I had to spend a whole more time fiddling around with it to get it to clear the heat shield. The black plastic thing behind the oil feed pipe is the water feed to the oil/water interchange cooler (or whatever it's called). The heat shield goes in front of the oil pipe and the water pipes to try to keep some of the turbo heat from them.
DSC04409
DSC04425
DSC04410
Here is the heat shield in place. There is an aluminium angle bolted underneath the exhaust manifold adapter and the heat shield is riveted to another piece of angle and the 2 go together to allow removal and allow me to manufacture it. I also got the aluminium angle for nothing.
DSC04415
the oil drain from the turbo used to go into a plate which is now mounted behind the heat shield. You can just see the hole to which the plate was attached, in this picture to the left of the black pipes, stuffed with polythene. It is also to be seen just poking out between the heat shield and the oil feed pipe in the picture above.
DSC04406
I will post another picture of that later but he does now become a breather. Although it looks like the oil drain (which is above the right-hand black pipe which is in the background) would go into the orifice which is stuffed with polythene, it’s the angle of the photograph that makes it look like that, in actual fact it wouldn’t. Therefore, the oil drain has to go into the dipstick tube which is stuffed with blue paper by the front engine pulley.
You can also see the very slight bend on the wastegate turbo actuator mounting plate which was needed to line up the actuator mounting rod.
Here is a view of the pipes in place which just needs a rubber joining piece. You can also see the turbo wastegate actuator plate and the heat shield.
DSC04424
watch this space.
I had the engine mounting plate plasma cut. I wanted to compare with laser cutting. Yes, I could have cut them out myself quite quickly using a 1 mm stainless steel type material cutting disc in an angle grinder and it would have been quicker than making them but firstly, I needed the sheet steel (which I didn’t have) and secondly, I didn’t want the grit and dust everywhere. I have had enough of that.
I did have the pattern for them drawn in CAD and as I did with the exhaust manifold adapter, I stuck the full-size PDF of the CAD drawing onto the plate, marked through the holes and drilled. You can see the remnants of the paper drawing in this photograph of the left-hand engine mount.
The round steel through the frame lug is simply a piece of bar for lining up purposes. There is yet to be a boss welded onto the triangular plate and the engine mountings in the lugs which are metalastic type, I’m going to buy new ones. The old ones were 30 years old and in any event, they had got a little “warm” (to say the least (!) when I heated the tubes up for bending.
Here is the left-hand one


still the Left-hand one. The thick plate/casting you can see under the mounting is part of the original Smart. There was an additional lug on the front which I cut off which is why the front is now a flat face. The alternative was to mount the 8 mm plate straight onto the engine block but that would have meant a long boss on the steel plate which would then have need a triangulation. I think the original Smart lump, although heavy, does a good job.

the right-hand one



I had removed the triangular braces which go in here to facilitate bending the front frame down tube. Here are my new and somewhat larger ones. The hole in the centre is just for lightening and aesthetic purposes. The plates are 3 mm which in hindsight is probably a little heavy. Still, I’m not going to get them remade in 2 mm.

I have mentioned many times that the exhaust manifold needed turning upside down. This is probably involved as much work and fannying around as any other single job.
When the turbo is turned upside down, the oil feed pipe that you see here had to moved to the top and the drain to the bottom. This photograph is in the relocated position.

Therefore, you have to remove the turbine housing (the alloy part) turn the turbo through 180° ° approximately. This then means that the wastegate actuator is in the wrong place and it won’t fit on the original lugs. I therefore had the circular plate laser cut from 4 mm stainless steel to remount the actuator. The reason for the rather odd bump on the outside is that I wasn’t quite sure where the actuator would fit so I left a chunk of extra metal so that I could play around with where the holes went. In the end, my design was way out. I also had to fit it twice in 2 different positions which accounts for the extra set of M 6 holes.

When it was first fitted the whole mechanism was quite stiff and it transpires that the actuator (for some bizarre reason) is on a slight angle. You can’t see very well in this photograph but there is a slight angle at the bottom of the circular plate. Vice + hammer + stainless steel part = bend.

You can’t see the oil feed pipe very well here but I had to spend a whole more time fiddling around with it to get it to clear the heat shield. The black plastic thing behind the oil feed pipe is the water feed to the oil/water interchange cooler (or whatever it's called). The heat shield goes in front of the oil pipe and the water pipes to try to keep some of the turbo heat from them.



Here is the heat shield in place. There is an aluminium angle bolted underneath the exhaust manifold adapter and the heat shield is riveted to another piece of angle and the 2 go together to allow removal and allow me to manufacture it. I also got the aluminium angle for nothing.

the oil drain from the turbo used to go into a plate which is now mounted behind the heat shield. You can just see the hole to which the plate was attached, in this picture to the left of the black pipes, stuffed with polythene. It is also to be seen just poking out between the heat shield and the oil feed pipe in the picture above.

I will post another picture of that later but he does now become a breather. Although it looks like the oil drain (which is above the right-hand black pipe which is in the background) would go into the orifice which is stuffed with polythene, it’s the angle of the photograph that makes it look like that, in actual fact it wouldn’t. Therefore, the oil drain has to go into the dipstick tube which is stuffed with blue paper by the front engine pulley.
You can also see the very slight bend on the wastegate turbo actuator mounting plate which was needed to line up the actuator mounting rod.
Here is a view of the pipes in place which just needs a rubber joining piece. You can also see the turbo wastegate actuator plate and the heat shield.

watch this space.
Last edited by touchwoodsden on Sun Feb 21, 2016 10:55 pm, edited 1 time in total.
Merc Estate
BRA CX 3
2 CV Dolly
2 x 250 MZs
1 x 125 4 stroke MZ
2 x 301 MZ
1 x Enfield Himalayan
1x Monkey bike
1 x Honda CT125
1 x Campervan Vivaro
1 x MZ Es250/1 and sidecar
1 x Cat
2 x Parrots
BRA CX 3
2 CV Dolly
2 x 250 MZs
1 x 125 4 stroke MZ
2 x 301 MZ
1 x Enfield Himalayan
1x Monkey bike
1 x Honda CT125
1 x Campervan Vivaro
1 x MZ Es250/1 and sidecar
1 x Cat
2 x Parrots
- Crazymanneil
- Site Admin
- Posts: 566
- Joined: Sat Dec 02, 2006 10:10 pm
- Location: Bangor, Northern Ireland
- Contact:
Re: The FrankenBrick Smart BMW build
Great thread. You might already know this but make sure not to do any welding with the ecu in the bike.
Neil
Neil
Smart engined 800cc turbo diesel triumph tiger. 100mpg (imp)
Belfast to Kathmandu overland, 2010/2011 - http://www.suckindiesel.com
Bangkok to Sydney ???
Belfast to Kathmandu overland, 2010/2011 - http://www.suckindiesel.com
Bangkok to Sydney ???
-
- I luv the smell of Diesel...
- Posts: 224
- Joined: Sat Oct 24, 2015 2:20 pm
- Location: North Wales, UK
Re: The FrankenBrick Smart BMW build
Thank Neil. I did indeed know. It hasnt even been plugged in yet!Crazymanneil wrote:Great thread. You might already know this but make sure not to do any welding with the ecu in the bike.
Neil
Lots of wiring to do still. More frame and engine mounting progress today. I think frame is almost ready for powder coating.
Pics to follow late or tomorrow.
JM
Merc Estate
BRA CX 3
2 CV Dolly
2 x 250 MZs
1 x 125 4 stroke MZ
2 x 301 MZ
1 x Enfield Himalayan
1x Monkey bike
1 x Honda CT125
1 x Campervan Vivaro
1 x MZ Es250/1 and sidecar
1 x Cat
2 x Parrots
BRA CX 3
2 CV Dolly
2 x 250 MZs
1 x 125 4 stroke MZ
2 x 301 MZ
1 x Enfield Himalayan
1x Monkey bike
1 x Honda CT125
1 x Campervan Vivaro
1 x MZ Es250/1 and sidecar
1 x Cat
2 x Parrots
-
- I luv the smell of Diesel...
- Posts: 224
- Joined: Sat Oct 24, 2015 2:20 pm
- Location: North Wales, UK
Re: The FrankenBrick Smart BMW build
a little time today on the lathe, then tacked things up with my little welder and borrowed a mates big welder and workshop to do the “big welding”
Left hand engine mounting.
DSC04427
Right-hand engine mounting.
DSC04432
DSC04429
Covering the bell housing with 1 mm sheet steel. By the time it is boxed in all-round, it’s going to be very rigid. I’m going to have to remove it to tack the rest of the sheet on.
DSC04435
There is going to have to be a removable cover here because the bolts which hold the starter motor on go through the 2 holes you can see here at the top and bottom of the starter motor “hump”.
I did have a look at trying to bolt the starter on from the starter side (outside) but I don't think it's going to be possible.
DSC04436
These plates form the platform for relays and ECU. It has a polycarbonate sheet on it which everything is mounted to. It is hidden behind the side panels. Must tidy bench.
DSC04437
Front frame triangulation (sorry, out of focus)
DSC04438
These little brackets at the front of the down tubes will have the top radiator mounting attached to them. The long rectangular blocks going down the side, with three holes in are tapped M6 and I will use if I decide to put the fairing back on. The original brackets were removed when the frame tubes were heated for bending.
DSC04439
Left hand engine mounting.

Right-hand engine mounting.


Covering the bell housing with 1 mm sheet steel. By the time it is boxed in all-round, it’s going to be very rigid. I’m going to have to remove it to tack the rest of the sheet on.

There is going to have to be a removable cover here because the bolts which hold the starter motor on go through the 2 holes you can see here at the top and bottom of the starter motor “hump”.
I did have a look at trying to bolt the starter on from the starter side (outside) but I don't think it's going to be possible.

These plates form the platform for relays and ECU. It has a polycarbonate sheet on it which everything is mounted to. It is hidden behind the side panels. Must tidy bench.

Front frame triangulation (sorry, out of focus)

These little brackets at the front of the down tubes will have the top radiator mounting attached to them. The long rectangular blocks going down the side, with three holes in are tapped M6 and I will use if I decide to put the fairing back on. The original brackets were removed when the frame tubes were heated for bending.

Merc Estate
BRA CX 3
2 CV Dolly
2 x 250 MZs
1 x 125 4 stroke MZ
2 x 301 MZ
1 x Enfield Himalayan
1x Monkey bike
1 x Honda CT125
1 x Campervan Vivaro
1 x MZ Es250/1 and sidecar
1 x Cat
2 x Parrots
BRA CX 3
2 CV Dolly
2 x 250 MZs
1 x 125 4 stroke MZ
2 x 301 MZ
1 x Enfield Himalayan
1x Monkey bike
1 x Honda CT125
1 x Campervan Vivaro
1 x MZ Es250/1 and sidecar
1 x Cat
2 x Parrots
-
- I luv the smell of Diesel...
- Posts: 224
- Joined: Sat Oct 24, 2015 2:20 pm
- Location: North Wales, UK
Front engine mounting bushes.
I am debating what to do about the front engine mounting bushes. In the original BMW motorcycle, they are metalastic albeit without a fantastic amount of rubber in. What is odd is that the whole engine gearbox assembly is held in with 4 x M 10 bolts, 2 at the rear on top of the gearbox and 2 at the front which are the ones which have the bushes in and which I made yesterday. It seems odd that 2 of the engine mountings have some slight movement and 2 of the more rigid albeit they are a couple of feet apart.
The original bushes from front engine mountings got rather hot when I was bending the frame tubes so they are gone and I’m now deciding what to do.
I can’t help feeling BMW must have done this for a reason. So the question is, do I get 2 new BMW bushes (assuming they are available) or, do I fill the frame lugs with steel bushes and make the front rigid as the rear is or (I think this is my favoured option at the moment), make up some of my own bushes but with Nylon 66 rather than rubber. It will have the tiniest tiniest amount of resilience.
Thoughts?
The original bushes from front engine mountings got rather hot when I was bending the frame tubes so they are gone and I’m now deciding what to do.
I can’t help feeling BMW must have done this for a reason. So the question is, do I get 2 new BMW bushes (assuming they are available) or, do I fill the frame lugs with steel bushes and make the front rigid as the rear is or (I think this is my favoured option at the moment), make up some of my own bushes but with Nylon 66 rather than rubber. It will have the tiniest tiniest amount of resilience.
Thoughts?
Merc Estate
BRA CX 3
2 CV Dolly
2 x 250 MZs
1 x 125 4 stroke MZ
2 x 301 MZ
1 x Enfield Himalayan
1x Monkey bike
1 x Honda CT125
1 x Campervan Vivaro
1 x MZ Es250/1 and sidecar
1 x Cat
2 x Parrots
BRA CX 3
2 CV Dolly
2 x 250 MZs
1 x 125 4 stroke MZ
2 x 301 MZ
1 x Enfield Himalayan
1x Monkey bike
1 x Honda CT125
1 x Campervan Vivaro
1 x MZ Es250/1 and sidecar
1 x Cat
2 x Parrots
- coachgeo
- I luv the smell of Diesel...
- Posts: 2002
- Joined: Sun Feb 22, 2009 6:00 am
- Location: USA Ohio, Above Cincinnati, Close to Dayton
Re: Front engine mounting bushes.
Most definitely uses bushes. the diesel will vibrate more than the original engine so bushes will be your friend. Also, will reduce potential of metal fatigue on the frame and new items you've welded on.touchwoodsden wrote:....
The original bushes from front engine mountings got rather hot when I was bending the frame tubes so they are gone and I’m now deciding what to do.
I can’t help feeling BMW must have done this for a reason. So the question is, do I get 2 new BMW bushes (assuming they are available) or, do I fill the frame lugs with steel bushes and make the front rigid as the rear is or (I think this is my favoured option at the moment), make up some of my own bushes but with Nylon 66 rather than rubber. It will have the tiniest tiniest amount of resilience.
Thoughts?
-
- I luv the smell of Diesel...
- Posts: 224
- Joined: Sat Oct 24, 2015 2:20 pm
- Location: North Wales, UK
Re: Front engine mounting bushes.
coachgeo wrote:Most definitely uses bushes. the diesel will vibrate more than the original engine so bushes will be your friend. Also, will reduce potential of metal fatigue on the frame and new items you've welded on.touchwoodsden wrote:....
The original bushes from front engine mountings got rather hot when I was bending the frame tubes so they are gone and I’m now deciding what to do.
I can’t help feeling BMW must have done this for a reason. So the question is, do I get 2 new BMW bushes (assuming they are available) or, do I fill the frame lugs with steel bushes and make the front rigid as the rear is or (I think this is my favoured option at the moment), make up some of my own bushes but with Nylon 66 rather than rubber. It will have the tiniest tiniest amount of resilience.
Thoughts?
My thoughts too BUT there are no bushes in frame in the 2 rear mounts, just the front 2 which seems odd
Merc Estate
BRA CX 3
2 CV Dolly
2 x 250 MZs
1 x 125 4 stroke MZ
2 x 301 MZ
1 x Enfield Himalayan
1x Monkey bike
1 x Honda CT125
1 x Campervan Vivaro
1 x MZ Es250/1 and sidecar
1 x Cat
2 x Parrots
BRA CX 3
2 CV Dolly
2 x 250 MZs
1 x 125 4 stroke MZ
2 x 301 MZ
1 x Enfield Himalayan
1x Monkey bike
1 x Honda CT125
1 x Campervan Vivaro
1 x MZ Es250/1 and sidecar
1 x Cat
2 x Parrots
-
- I luv the smell of Diesel...
- Posts: 224
- Joined: Sat Oct 24, 2015 2:20 pm
- Location: North Wales, UK
Re: The FrankenBrick Smart BMW build
I don’t like the idea of the oil all flying to the front of the engine under heavy braking or all rushing to the back under fierce acceleration (some hope!) So, while the sump is off, I decided to fit a baffle .
Here is the cardboard template in place. It has to be over at a slight angle towards the bottom to clear the oil pickup tube.
DSC04441
It doesn’t matter how many times you drain the engine, there’s always more oil to come out.
DSC04448
DSC04447
This is the 1 mm steel sheet going over the outside of the adapter plates. I’m cutting it into strips so as not to distort the basic structure. Then it’s going to be tack welded at 25 mm intervals all round and I’m going to fill the gaps with body filler before painting. Okay, it might crack but it is unlikely to fall out because I’m going to sandblast the gaps first to give a good key. I want to make sure that the whole structure doesn’t distort which is why it’s only being tack welded. Although it will form a sort of monocoque, it also got to look relatively pretty. It looks a mess now but I’m quite happy that it will look absolutely fine when filled and fettled and painted.
DSC04443
DSC04445
Here is the cardboard template in place. It has to be over at a slight angle towards the bottom to clear the oil pickup tube.

It doesn’t matter how many times you drain the engine, there’s always more oil to come out.


This is the 1 mm steel sheet going over the outside of the adapter plates. I’m cutting it into strips so as not to distort the basic structure. Then it’s going to be tack welded at 25 mm intervals all round and I’m going to fill the gaps with body filler before painting. Okay, it might crack but it is unlikely to fall out because I’m going to sandblast the gaps first to give a good key. I want to make sure that the whole structure doesn’t distort which is why it’s only being tack welded. Although it will form a sort of monocoque, it also got to look relatively pretty. It looks a mess now but I’m quite happy that it will look absolutely fine when filled and fettled and painted.


Merc Estate
BRA CX 3
2 CV Dolly
2 x 250 MZs
1 x 125 4 stroke MZ
2 x 301 MZ
1 x Enfield Himalayan
1x Monkey bike
1 x Honda CT125
1 x Campervan Vivaro
1 x MZ Es250/1 and sidecar
1 x Cat
2 x Parrots
BRA CX 3
2 CV Dolly
2 x 250 MZs
1 x 125 4 stroke MZ
2 x 301 MZ
1 x Enfield Himalayan
1x Monkey bike
1 x Honda CT125
1 x Campervan Vivaro
1 x MZ Es250/1 and sidecar
1 x Cat
2 x Parrots
-
- I luv the smell of Diesel...
- Posts: 517
- Joined: Sun Dec 10, 2006 8:35 pm
- Location: STAFFORDSHIRE ENGLAND
Re: The FrankenBrick Smart BMW build
I think the baffle is a good idea, by removing the wedge off the bottom haven't you reduced the capacity? If so wouldn't it be good to also add some capacity at this stage that is if you have some room.
Sam
-
- I luv the smell of Diesel...
- Posts: 224
- Joined: Sat Oct 24, 2015 2:20 pm
- Location: North Wales, UK
Re: The FrankenBrick Smart BMW build
Yes, removing the wedge has reduced the capacity and it would indeed be a good idea to increase the capacity. I have already been down this in my mind.sbrumby wrote:I think the baffle is a good idea, by removing the wedge off the bottom haven't you reduced the capacity? If so wouldn't it be good to also add some capacity at this stage that is if you have some room.
There are a few ways of doing that, increase the width or length of the sump but that’s totally impractical because you’re stuck with the attachment flange. You could make it deeper but then again there is the problem of it hitting the ground which is why the wedge was cut off in the first place.
The other alternative B to square off the wedge. Which is what I will do when I make my next sump in stainless steel. I already have the flange cut out and it just needs the “box” making but as it’s stainless, it’s going to have to be done by somebody else.
At the moment, it has an oil/water oil cooler and I could replace that with an air/oil cooler which along with the pipes would add extra capacity. mean making up an adapter plate to go onto the engine but I can’t see that being a big deal. Finding somewhere to put the oil cooler might be more problematical but it’s not the biggest job that has been overcome.
However I have to ask myself “is it worth it”.
Eva Track used a circular bottom sump which looks to me as though it has less capacity than this one although because of the partial wedge on mine, it’s about the same probably. You have to bear in mind also that the oil will get changed more frequently in this than ever it would in the car and it will not be working as hard in the car because it’s not carrying as much weight.
I spent 45 minutes in the shed this morning and have all the metal now tack welded in place on the adapter. I will give it a good clean up tonight. I was conscious last night of making a noise in my garage with the angle grinder so didn’t want to carry on late. I have fantastic neighbours and I don’t want to spoil that. This evening should see the sump finished and in place and the adapter metalwork virtually finished.
Feedback and input is always welcome because I’m certain there are lots of things which I haven’t even thought of yet.
Merc Estate
BRA CX 3
2 CV Dolly
2 x 250 MZs
1 x 125 4 stroke MZ
2 x 301 MZ
1 x Enfield Himalayan
1x Monkey bike
1 x Honda CT125
1 x Campervan Vivaro
1 x MZ Es250/1 and sidecar
1 x Cat
2 x Parrots
BRA CX 3
2 CV Dolly
2 x 250 MZs
1 x 125 4 stroke MZ
2 x 301 MZ
1 x Enfield Himalayan
1x Monkey bike
1 x Honda CT125
1 x Campervan Vivaro
1 x MZ Es250/1 and sidecar
1 x Cat
2 x Parrots
-
- I luv the smell of Diesel...
- Posts: 224
- Joined: Sat Oct 24, 2015 2:20 pm
- Location: North Wales, UK
Re: The FrankenBrick Smart BMW build
I don’t know if anyone has seen this thread on Facebook but there is a guy, Joe Lamont in Kilmarnock is putting a Smart into a K 100. He is using the Specialist Components ECU. The engine is running the bike is not riding yet.
https://www.facebook.com/photo.php?fbid ... =3&theater
joe lamont
He is having the engine canted over like this one from Germany.
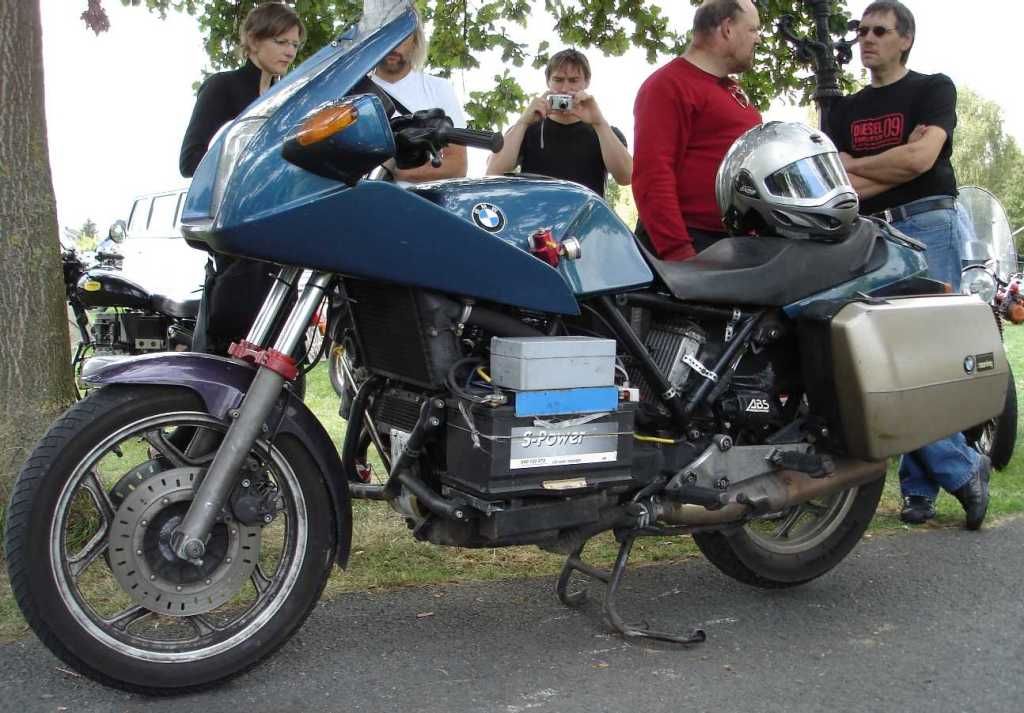
We have exchanged a few very brief messages on Facebook.
Regards
https://www.facebook.com/photo.php?fbid ... =3&theater

He is having the engine canted over like this one from Germany.
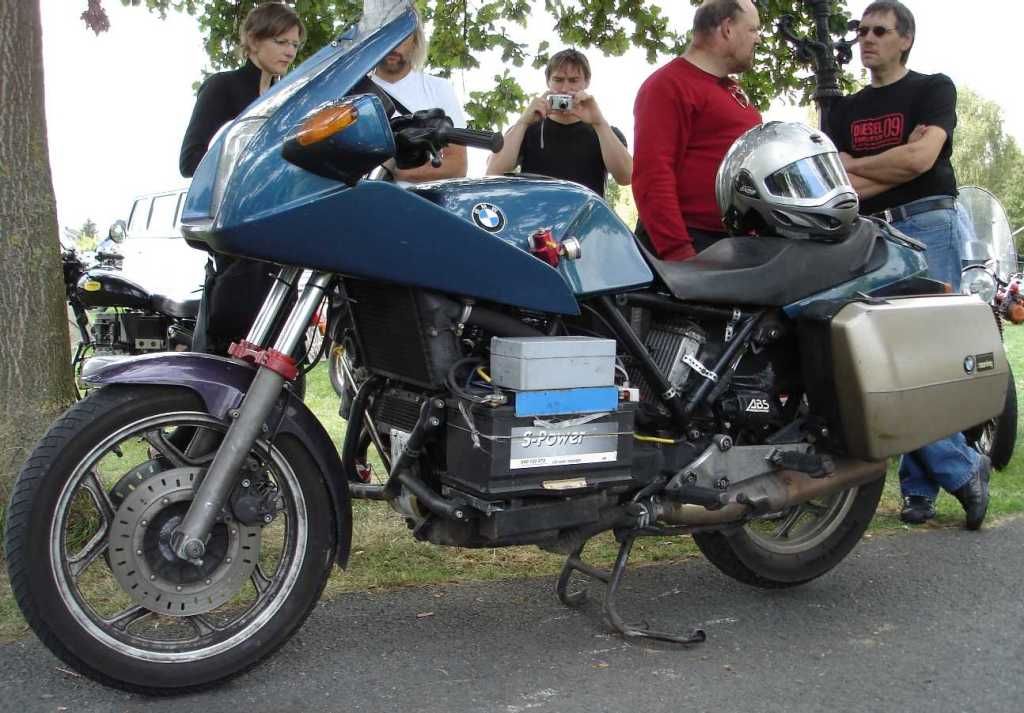
We have exchanged a few very brief messages on Facebook.
Regards
Merc Estate
BRA CX 3
2 CV Dolly
2 x 250 MZs
1 x 125 4 stroke MZ
2 x 301 MZ
1 x Enfield Himalayan
1x Monkey bike
1 x Honda CT125
1 x Campervan Vivaro
1 x MZ Es250/1 and sidecar
1 x Cat
2 x Parrots
BRA CX 3
2 CV Dolly
2 x 250 MZs
1 x 125 4 stroke MZ
2 x 301 MZ
1 x Enfield Himalayan
1x Monkey bike
1 x Honda CT125
1 x Campervan Vivaro
1 x MZ Es250/1 and sidecar
1 x Cat
2 x Parrots
-
- I luv the smell of Diesel...
- Posts: 224
- Joined: Sat Oct 24, 2015 2:20 pm
- Location: North Wales, UK
Re: The FrankenBrick Smart BMW build
I spent a bit of time this evening cleaning up the welds on the engine/gearbox/bell housing/adapter. I am rather pleased with it. I then spent a bit of time sandblasting it to give a key for the filler with which I’m going to fill the cracks. As I said earlier, if it comes loose, I’m no worse off than I was before. I don’t cherish the thought of fully welding each of the seams and to be honest, I can’t see the point. Anyway, unless it has to, it is not happening!
DSC04464
You may recall that there are 2 bolts which hold the starter motor in which go through these holes.
DSC04453
I need access to them so I left “windows” (nothing to do with Bill Gates) through which to access the starter motor retaining bolts.
I then made these little “doors” which attach with 2 x M4 button head sockets which are tapped into the engine block flanged of the adapter. You can just see the 2 tapped holes in these pictures.
DSC04458
I’m quite pleased with those little doors also. Yes, they could have been better but they took half an hour to make and to fit and I’m quite happy with them.
DSC04473
And here is the sump baffle in place which actually slopes the opposite way than it did in the earlier photograph in a previous post with the cardboard template in place. Mea Culpa got it sloping the wrong way in cardboard. DOH.
DSC04465
I’m going to do a bit more work on the frame tomorrow because I want to get that off to the powder coaters. I’ve also got a lot of flatting down to do on the plastics of the original bike and of course the fuel tank although, as the tank is BMW alloy, I’m wondering what it would look like stripped and polished.
I also have the front forks to strip because the bottom legs really do need a decent paint job.
I am waiting on the high ratio gears for the gearbox which could be several months away so progress towards completion of the project may grind to a halt shortly. Still, the hiatus will give me some time to get the rest of things in order and stop me rushing things which should not be rushed.
I have someone who was agreed to do the exhaust for me in exchange for a little bit of work which he needs doing by me so that might be a good result.

You may recall that there are 2 bolts which hold the starter motor in which go through these holes.

I need access to them so I left “windows” (nothing to do with Bill Gates) through which to access the starter motor retaining bolts.
I then made these little “doors” which attach with 2 x M4 button head sockets which are tapped into the engine block flanged of the adapter. You can just see the 2 tapped holes in these pictures.

I’m quite pleased with those little doors also. Yes, they could have been better but they took half an hour to make and to fit and I’m quite happy with them.

And here is the sump baffle in place which actually slopes the opposite way than it did in the earlier photograph in a previous post with the cardboard template in place. Mea Culpa got it sloping the wrong way in cardboard. DOH.

I’m going to do a bit more work on the frame tomorrow because I want to get that off to the powder coaters. I’ve also got a lot of flatting down to do on the plastics of the original bike and of course the fuel tank although, as the tank is BMW alloy, I’m wondering what it would look like stripped and polished.
I also have the front forks to strip because the bottom legs really do need a decent paint job.
I am waiting on the high ratio gears for the gearbox which could be several months away so progress towards completion of the project may grind to a halt shortly. Still, the hiatus will give me some time to get the rest of things in order and stop me rushing things which should not be rushed.
I have someone who was agreed to do the exhaust for me in exchange for a little bit of work which he needs doing by me so that might be a good result.
Merc Estate
BRA CX 3
2 CV Dolly
2 x 250 MZs
1 x 125 4 stroke MZ
2 x 301 MZ
1 x Enfield Himalayan
1x Monkey bike
1 x Honda CT125
1 x Campervan Vivaro
1 x MZ Es250/1 and sidecar
1 x Cat
2 x Parrots
BRA CX 3
2 CV Dolly
2 x 250 MZs
1 x 125 4 stroke MZ
2 x 301 MZ
1 x Enfield Himalayan
1x Monkey bike
1 x Honda CT125
1 x Campervan Vivaro
1 x MZ Es250/1 and sidecar
1 x Cat
2 x Parrots
-
- I luv the smell of Diesel...
- Posts: 517
- Joined: Sun Dec 10, 2006 8:35 pm
- Location: STAFFORDSHIRE ENGLAND
Re: The FrankenBrick Smart BMW build
Looking good, Have you checked sump is oil tight? best way if you haven't is with petrol, a jam jar full would be enough.
Sam
-
- I luv the smell of Diesel...
- Posts: 224
- Joined: Sat Oct 24, 2015 2:20 pm
- Location: North Wales, UK
Re: The FrankenBrick Smart BMW build
I had a thought. Lead loading (that was). Will try using (now) lead free plumbers solder to fill the gaps. Technique used by panel beaters in the days before body filler.
I have Bakers Fluid (flux) for steel. Watch this space.
Update.
I spent 45 minutes with a blow lamp and some solder. It must be quite old solder as it says "contains lead" so when I sanded it off, I wore a respirator.
It is filled the gaps quite nicely and is going to obviously stick better than filler.
I haven't quite finished it yet because I've still got some welding to do around the pillars on the inside. I couldn't do it when it was on the engine/gearbox.
As soon as it's finished, I'll post some photographs
I have Bakers Fluid (flux) for steel. Watch this space.
Update.
I spent 45 minutes with a blow lamp and some solder. It must be quite old solder as it says "contains lead" so when I sanded it off, I wore a respirator.
It is filled the gaps quite nicely and is going to obviously stick better than filler.
I haven't quite finished it yet because I've still got some welding to do around the pillars on the inside. I couldn't do it when it was on the engine/gearbox.
As soon as it's finished, I'll post some photographs
Merc Estate
BRA CX 3
2 CV Dolly
2 x 250 MZs
1 x 125 4 stroke MZ
2 x 301 MZ
1 x Enfield Himalayan
1x Monkey bike
1 x Honda CT125
1 x Campervan Vivaro
1 x MZ Es250/1 and sidecar
1 x Cat
2 x Parrots
BRA CX 3
2 CV Dolly
2 x 250 MZs
1 x 125 4 stroke MZ
2 x 301 MZ
1 x Enfield Himalayan
1x Monkey bike
1 x Honda CT125
1 x Campervan Vivaro
1 x MZ Es250/1 and sidecar
1 x Cat
2 x Parrots
-
- I luv the smell of Diesel...
- Posts: 103
- Joined: Sun Feb 08, 2015 7:08 am
- Location: Philippinen
Re: The FrankenBrick Smart BMW build
No! Oil will leak from holes to small for petrol. Take diesel.sbrumby wrote:Looking good, Have you checked sump is oil tight? best way if you haven't is with petrol, a jam jar full would be enough.
And, is the flow beween the 2 chambers good enough? I had it once on an old BMW V8 that the oilpressure dropped at hihg RPM because the oil did not paased the buffer fast enough.
Alex
-
- I luv the smell of Diesel...
- Posts: 137
- Joined: Mon Aug 05, 2013 7:26 pm
- Location: Crossens, Southport, UK.
Re: The FrankenBrick Smart BMW build
Shouldn't there at least a couple of holes in the baffle plate to allow oil to pass through? From the pictures it doesn't look like there are any big enough gaps for the oil to pass from one side to the other when the engine is running normally.
Building the bike. Top of my list, bottom of the wife's.
-
- I luv the smell of Diesel...
- Posts: 517
- Joined: Sun Dec 10, 2006 8:35 pm
- Location: STAFFORDSHIRE ENGLAND
Re: The FrankenBrick Smart BMW build
Alex I don't quite know what you are on about, petrol is thinner than diesel and any weak spot petrol will find it.
Sam
-
- I luv the smell of Diesel...
- Posts: 224
- Joined: Sat Oct 24, 2015 2:20 pm
- Location: North Wales, UK
Re: The FrankenBrick Smart BMW build
Hot oil is very thin of course. There are 2 scallops at the bottom and a small gap all around. I can easily make scallops bigger. No point in having holes in the middle of the plate as they are need at the bottom for oil change.bf109v7 wrote:No! Oil will leak from holes to small for petrol. Take diesel.sbrumby wrote:Looking good, Have you checked sump is oil tight? best way if you haven't is with petrol, a jam jar full would be enough.
And, is the flow beween the 2 chambers good enough? I had it once on an old BMW V8 that the oilpressure dropped at hihg RPM because the oil did not paased the buffer fast enough.
Alex
I disagree that diesel or hot oil will find holes better than petrol. I actually used both and celly thinners one after the other. Yes there were leaks, but not now.
Thanks for input
Merc Estate
BRA CX 3
2 CV Dolly
2 x 250 MZs
1 x 125 4 stroke MZ
2 x 301 MZ
1 x Enfield Himalayan
1x Monkey bike
1 x Honda CT125
1 x Campervan Vivaro
1 x MZ Es250/1 and sidecar
1 x Cat
2 x Parrots
BRA CX 3
2 CV Dolly
2 x 250 MZs
1 x 125 4 stroke MZ
2 x 301 MZ
1 x Enfield Himalayan
1x Monkey bike
1 x Honda CT125
1 x Campervan Vivaro
1 x MZ Es250/1 and sidecar
1 x Cat
2 x Parrots
-
- I luv the smell of Diesel...
- Posts: 103
- Joined: Sun Feb 08, 2015 7:08 am
- Location: Philippinen
Re: The FrankenBrick Smart BMW build
They found out when they started to build diesel airplanes. The tanks, which had no probems with petrol leaked the diesel.touchwoodsden wrote:I disagree that diesel or hot oil will find holes better than petrol. I actually used both and celly thinners one after the other. Yes there were leaks, but not now.bf109v7 wrote:No! Oil will leak from holes to small for petrol. Take diesel.sbrumby wrote:Looking good, Have you checked sump is oil tight? best way if you haven't is with petrol, a jam jar full would be enough.
Thanks for input
Also antifreese leaks much better than water, observe this when you check your cooling system.
Alex
-
- I luv the smell of Diesel...
- Posts: 224
- Joined: Sat Oct 24, 2015 2:20 pm
- Location: North Wales, UK
Re: The FrankenBrick Smart BMW build
Thanks but the sump isnt full of diesel but engine oil.
The ant freeze leak thing I was aware of and that petrol will leak when water wont due to the surface tension of the water. The AF acts as a wetting agent
The ant freeze leak thing I was aware of and that petrol will leak when water wont due to the surface tension of the water. The AF acts as a wetting agent
Merc Estate
BRA CX 3
2 CV Dolly
2 x 250 MZs
1 x 125 4 stroke MZ
2 x 301 MZ
1 x Enfield Himalayan
1x Monkey bike
1 x Honda CT125
1 x Campervan Vivaro
1 x MZ Es250/1 and sidecar
1 x Cat
2 x Parrots
BRA CX 3
2 CV Dolly
2 x 250 MZs
1 x 125 4 stroke MZ
2 x 301 MZ
1 x Enfield Himalayan
1x Monkey bike
1 x Honda CT125
1 x Campervan Vivaro
1 x MZ Es250/1 and sidecar
1 x Cat
2 x Parrots
-
- I luv the smell of Diesel...
- Posts: 224
- Joined: Sat Oct 24, 2015 2:20 pm
- Location: North Wales, UK
Re: The FrankenBrick Smart BMW build
touchwoodsden wrote:I don’t like the idea of the oil all flying to the front of the engine under heavy braking or all rushing to the back under fierce acceleration (some hope!) So, while the sump is off, I decided to fit a baffle .
Here is the cardboard template in place. It has to be over at a slight angle towards the bottom to clear the oil pickup tube.
DSC04441
It doesn’t matter how many times you drain the engine, there’s always more oil to come out.
DSC04448
DSC04447
This is the 1 mm steel sheet going over the outside of the adapter plates. I’m cutting it into strips so as not to distort the basic structure. Then it’s going to be tack welded at 25 mm intervals all round and I’m going to fill the gaps with body filler before painting. Okay, it might crack but it is unlikely to fall out because I’m going to sandblast the gaps first to give a good key. I want to make sure that the whole structure doesn’t distort which is why it’s only being tack welded. Although it will form a sort of monocoque, it also got to look relatively pretty. It looks a mess now but I’m quite happy that it will look absolutely fine when filled and fettled and painted.
DSC04443
DSC04445
Merc Estate
BRA CX 3
2 CV Dolly
2 x 250 MZs
1 x 125 4 stroke MZ
2 x 301 MZ
1 x Enfield Himalayan
1x Monkey bike
1 x Honda CT125
1 x Campervan Vivaro
1 x MZ Es250/1 and sidecar
1 x Cat
2 x Parrots
BRA CX 3
2 CV Dolly
2 x 250 MZs
1 x 125 4 stroke MZ
2 x 301 MZ
1 x Enfield Himalayan
1x Monkey bike
1 x Honda CT125
1 x Campervan Vivaro
1 x MZ Es250/1 and sidecar
1 x Cat
2 x Parrots
-
- I luv the smell of Diesel...
- Posts: 224
- Joined: Sat Oct 24, 2015 2:20 pm
- Location: North Wales, UK
K100 front engine mounting bushes
Fek me. The bushes are £26 EACH !!!!!! No cheaper in Germany.
https://www.motorworks.co.uk/vlive/Shop ... &x=21&y=17
I think I will be making some from nylon or going solid!
https://www.motorworks.co.uk/vlive/Shop ... &x=21&y=17
I think I will be making some from nylon or going solid!
Merc Estate
BRA CX 3
2 CV Dolly
2 x 250 MZs
1 x 125 4 stroke MZ
2 x 301 MZ
1 x Enfield Himalayan
1x Monkey bike
1 x Honda CT125
1 x Campervan Vivaro
1 x MZ Es250/1 and sidecar
1 x Cat
2 x Parrots
BRA CX 3
2 CV Dolly
2 x 250 MZs
1 x 125 4 stroke MZ
2 x 301 MZ
1 x Enfield Himalayan
1x Monkey bike
1 x Honda CT125
1 x Campervan Vivaro
1 x MZ Es250/1 and sidecar
1 x Cat
2 x Parrots
-
- I luv the smell of Diesel...
- Posts: 103
- Joined: Sun Feb 08, 2015 7:08 am
- Location: Philippinen
Re: The FrankenBrick Smart BMW build
Here in the Philippinens they make all kind of rubber buchings from old truck tires. Real cheap.
What is the size of this bushig? It looks to me like the one Dnepr uses for the rear suspension bearing.
I am sure we can find rubber for a better price.
Alex
What is the size of this bushig? It looks to me like the one Dnepr uses for the rear suspension bearing.
I am sure we can find rubber for a better price.
Alex
-
- I luv the smell of Diesel...
- Posts: 224
- Joined: Sat Oct 24, 2015 2:20 pm
- Location: North Wales, UK
Re: The FrankenBrick Smart BMW build
I think I am going to have to do something else as I cant justify that costbf109v7 wrote:Here in the Philippinens they make all kind of rubber buchings from old truck tires. Real cheap.
What is the size of this bushig? It looks to me like the one Dnepr uses for the rear suspension bearing.
I am sure we can find rubber for a better price.
Alex
They are very hard rubber. These is a heavy steel bush in the centre which is 10.5mm bore, x 15 outisde dia. It is 24mm long There is a small flange on one end of the steel centre bush . The hole in the frame is 20mm dia. They are moulded in one piece, I took the bush out (blowlamp!) to measure size.

Merc Estate
BRA CX 3
2 CV Dolly
2 x 250 MZs
1 x 125 4 stroke MZ
2 x 301 MZ
1 x Enfield Himalayan
1x Monkey bike
1 x Honda CT125
1 x Campervan Vivaro
1 x MZ Es250/1 and sidecar
1 x Cat
2 x Parrots
BRA CX 3
2 CV Dolly
2 x 250 MZs
1 x 125 4 stroke MZ
2 x 301 MZ
1 x Enfield Himalayan
1x Monkey bike
1 x Honda CT125
1 x Campervan Vivaro
1 x MZ Es250/1 and sidecar
1 x Cat
2 x Parrots
-
- I luv the smell of Diesel...
- Posts: 224
- Joined: Sat Oct 24, 2015 2:20 pm
- Location: North Wales, UK
Re: The FrankenBrick Smart BMW build
A quiet night in (the workshop) tonight.
The bell housing adapter isn’t a piece of bodywork so it doesn’t need to be perfectly finished, after all, engine and gearbox are both castings. I think I might spray with some hammer finish aerosol.
I gave it a thin smear of body filler on the outside and then a lot of sanding and a lot of dust later, coat of zinc rich primer.
DSC04486
If ever you try to cram full, BMW K 100 panniers and forced them closed using the catches, expect it to break and then have to make replacements yourself. Just the 1 in my case.
DSC04480
The clutch is held on by M7 Torx screws which are high tensile. Have you ever tried to get M7 high tensile screws of any description?
I could have gone up to M8, or sleeve the holes down to M6, but, after much searching, I found these which were exactly the right length. You’ll never guess what they are.
Wrong.
They are Compomotive wheel split rim retaining bolts. They come with really heavy washers which are really ideal. From the bay of e.
DSC04489
The bell housing adapter isn’t a piece of bodywork so it doesn’t need to be perfectly finished, after all, engine and gearbox are both castings. I think I might spray with some hammer finish aerosol.
I gave it a thin smear of body filler on the outside and then a lot of sanding and a lot of dust later, coat of zinc rich primer.

If ever you try to cram full, BMW K 100 panniers and forced them closed using the catches, expect it to break and then have to make replacements yourself. Just the 1 in my case.

The clutch is held on by M7 Torx screws which are high tensile. Have you ever tried to get M7 high tensile screws of any description?
I could have gone up to M8, or sleeve the holes down to M6, but, after much searching, I found these which were exactly the right length. You’ll never guess what they are.
Wrong.
They are Compomotive wheel split rim retaining bolts. They come with really heavy washers which are really ideal. From the bay of e.

Merc Estate
BRA CX 3
2 CV Dolly
2 x 250 MZs
1 x 125 4 stroke MZ
2 x 301 MZ
1 x Enfield Himalayan
1x Monkey bike
1 x Honda CT125
1 x Campervan Vivaro
1 x MZ Es250/1 and sidecar
1 x Cat
2 x Parrots
BRA CX 3
2 CV Dolly
2 x 250 MZs
1 x 125 4 stroke MZ
2 x 301 MZ
1 x Enfield Himalayan
1x Monkey bike
1 x Honda CT125
1 x Campervan Vivaro
1 x MZ Es250/1 and sidecar
1 x Cat
2 x Parrots
-
- I luv the smell of Diesel...
- Posts: 103
- Joined: Sun Feb 08, 2015 7:08 am
- Location: Philippinen
Re: The FrankenBrick Smart BMW build
I was thinking of the bushin of Dnepr rear shockabsorber mounting, presst in the reaer swing. But this is inside 10,25, 22 long, but outside it has a steel ring vulcanised tu it with 28 outside. I dont know the pice, but it is cheap, I ordered 10 to have some at home.touchwoodsden wrote:I think I am going to have to do something else as I cant justify that costbf109v7 wrote:Here in the Philippinens they make all kind of rubber buchings from old truck tires. Real cheap.
What is the size of this bushig? It looks to me like the one Dnepr uses for the rear suspension bearing.
I am sure we can find rubber for a better price.
Alex
They are very hard rubber. These is a heavy steel bush in the centre which is 10.5mm bore, x 15 outisde dia. It is 24mm long There is a small flange on one end of the steel centre bush . The hole in the frame is 20mm dia. They are moulded in one piece, I took the bush out (blowlamp!) to measure size.
DSC04474
Alex
-
- I luv the smell of Diesel...
- Posts: 87
- Joined: Sat Dec 06, 2014 11:25 pm
- Location: Canada
Re: The FrankenBrick Smart BMW build
http://www.mcmaster.com/ A good place to shop for special fastners and hard to find parts.
- Tetronator
- I luv the smell of Diesel...
- Posts: 502
- Joined: Mon Apr 07, 2014 11:50 am
- Location: Amsterdam
- Contact:
Re: The FrankenBrick Smart BMW build
Alex is talking about these;bf109v7 wrote:I was thinking of the bushin of Dnepr rear shockabsorber mounting, presst in the reaer swing. But this is inside 10,25, 22 long, but outside it has a steel ring vulcanised tu it with 28 outside. I dont know the pice, but it is cheap, I ordered 10 to have some at home.touchwoodsden wrote:I think I am going to have to do something else as I cant justify that costbf109v7 wrote:Here in the Philippinens they make all kind of rubber buchings from old truck tires. Real cheap.
What is the size of this bushig? It looks to me like the one Dnepr uses for the rear suspension bearing.
I am sure we can find rubber for a better price.
Alex
They are very hard rubber. These is a heavy steel bush in the centre which is 10.5mm bore, x 15 outisde dia. It is 24mm long There is a small flange on one end of the steel centre bush . The hole in the frame is 20mm dia. They are moulded in one piece, I took the bush out (blowlamp!) to measure size.
DSC04474
Alex
http://www.ural-zentrale.de/en/swingarm ... bber-dnepr